一键完成不良分析‐超越红外显微镜概念的革新性解决方案
本文回顾了岛津的工程师为了贯彻自己的理念——让每一个人都能轻松地分析不良品的原因,在不良分析的三个重要工艺步骤“观察”、“测量”、“判断”实现自动化的技术发展轨迹。
20年的差距
矶圭祐
分析测试事业部技术部分析仪器小组
“这真的有必要吗?”那是2011年年初发生在岛津制作所三条工厂的一幕。土渕坚持不懈地追问技术部的矶,开发新型红外显微镜时为了提高分析的精度,是否真的有必要将摄像头的分辨率提高到现有机种的16倍以上。对矶来说,土渕比他年长十几岁分析方面的知识和技能水平也远在自己之上。即便如此,矶感觉有一条线他不能够妥协。
红外显微镜被用于医药品片剂上附着的异物、电子基板污垢的识别等不良分析中。利用红外线吸收、反射的方式,可在分子级别上确定对象的构成物质。例如,聚丙烯、丙烯酸是透明的塑料,在可见光下,即使观察细小的碎片也很难发现两者的区别。如果在红外显微镜下,就能呈现明显的差异。
岛津从20世纪80年代中期开始进军红外显微镜市场。1998年发售的AIM-8800凭借其稳定的性能,获得了众多客户的支持。自那之后的20年间,该机型也曾通过小幅度的版本升级提高了性能,但无法充分满足市场中急速的需求变化。
90年代的主要客户是大学、研究机构的专业分析人员,由于他们大多自主开发分析手法,因而对基本性能的提升是当时最大的需求。由于这一产品后来逐渐被用于制造电子元件、食品等时的品质管理、不良品原因的特定,专业人员以外的普通用户也开始增加了。于是,市场上需要一款操作简单的装置,这样即便不具备专业知识也能确保获得稳定的数据。
不想制造因循守旧的产品
于是,在2010年岛津组建了新型红外显微镜的开发小组。小组最开始讨论的是应该瞄准哪个市场。是和过去一样,面向要求基本性能的专业人员制造产品呢,还是面向最近不断增加的追求易用便捷的客户群,满足他们的需求呢?“既然要做,就不想制造因循守旧的产品。也正因如此,我们毅然选择了开拓新市场的道路”技术部的横田这样讲述当时的强烈决心。
从“零”开始的开发
横田佳澄
分析测试事业部技术部新事业开发推进小组
就这样,大家决定了产品开发的目标方向。但开发小组从一开始就碰壁了。“听起来像在开玩笑,当时我们四人谁都没有接触过红外显微镜”(横田)
现有机型是20年前开发的,当时的核心开发人员大多已经退休,能够参考的资料也几乎没有。召集来的开发小组成员原先各自负责不同的装置,因此,从各方面来说,都必须从零开始。
这个时候,为我们提供帮助的是全球应用开发中心(以下称GADC)。GADC聚集了负责应对来自岛津公司外部的分析咨询的专家,他们在日常业务中使用红外显微镜。开头提到的土渕(现任该中心光谱仪BU长)就是其中的一员。开发小组拍摄了土渕等专家用红外显微镜分析样本的情景,他们反复观看这一视频,自己也实际操作,从而理解了装置的使用方法。同时,土渕和GADC的成员多次询问了矶和开发小组的其它成员想要制造怎样的产品。其中,矶比较在意的就是高清摄像头。
“资源是有限的,如果不能准确地分配资源,项目就会停滞不前。深知客户要求的土渕给出的意见是很有道理的。但是,我们的决心是制造所有人都能简单操作的红外显微镜。在这一点上,我们没有让步”(矶)
另一方面,在大家反复实践分析过程时,开发小组注意到一个比较大的问题。通常,用红外显微镜观察时,首先会用光学显微镜观察对象物质,用胶带、记号笔在杂质、不良部位做记号,然后把对象物移到红外显微镜下,观察记号部分。
青位祐辅
分析测试事业部技术部成像小组
分析方面的专家可以轻松对准这一位置,但对于操作不熟练的人来说,寻找肉眼看不见的细微对象物,就像是苦行般的工程。因此,负责机械设计的马路(光谱仪BU)在倍率虽高但视野较窄的显微镜用摄像头之外,搭载了以与肉眼相同倍率进行观察的广角摄像头。并且,负责软件的青位(技术部)与同公司的基础技术研究所合作,开发出了对疑似不良部位进行图像识别并自动进行标记的软件。
“我们伤脑筋的地方也应该是用户伤脑筋的地方。因此,如何让所有人都能掌握专家的技能,正是我们需要研究思考的课题”(青位)
我们非常注重软件的使用感。在项目开始一年后的2012年,当试制机制成后,开发小组召集了对于分析装置的操作经验较少的员工,连日实施可用性测试,就使用感听取了大家的反馈。
“我们的目标是实现如智能手机应用软件般的操作便捷性。我们还对市售应用软件的用户界面进行了深度研究”(青位)
自动不良分析系统的完成
马路健
分析测试事业部光谱仪BU IR小组
在启动开发工作约五年后的2015年的年末,当时正在反复进行最终测试的马路的脑海里突然浮现出一句话:“‘这已经不是红外显微镜了’。当然,它确实是红外显微镜,为了尽可能对不良部位实施快速、正确的分析,我们倾注了大量心血。就在那时我意识到,其实我们是在制作一个‘自动不良分析系统’”
就这样,2016年5月我们推出了不良分析系统AIM-9000。
前所未有的易用性受到了大家的关注,过去将分析业务委托给专门业者的企业纷纷发来咨询。在实施品质管理时必不可少的产品检查装置的历史上,又增添了全新的一页。
注1:本文中所登载的被采访者的所属团体、职务名等皆为采访当时的情况。
注2:AIM-9000荣获具有国际权威性的德国设计奖项——红点设计奖 产品设计2018(Red Dot Design Award Product Design 2018)。
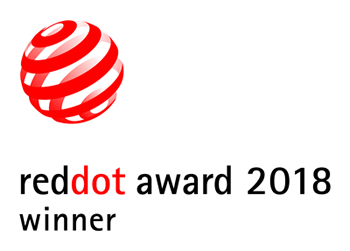
分析测试事业部技术部新事业开发推进小组
横田佳澄(右上)
分析测试事业部光谱仪BU IR小组
马路健(左上)
分析测试事业部技术部成像小组
青位祐辅(右下)
分析测试事业部技术部分析仪器小组
矶圭祐(左下)